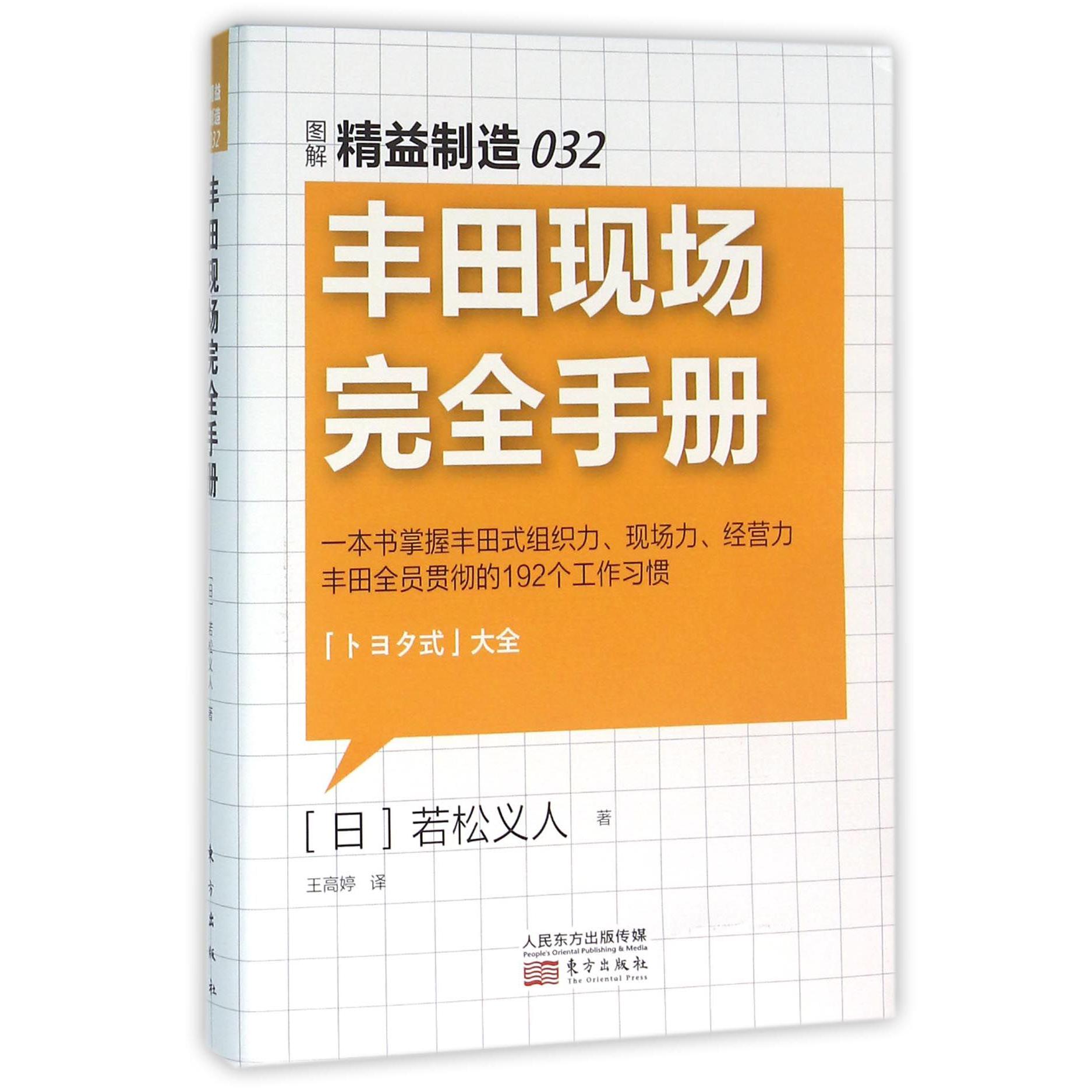
出版社: 东方
原售价: 46.00
折扣价: 29.90
折扣购买: 丰田现场完全手册(图解精益制造)
ISBN: 9787506089517
若松义人,1937年生,日本宫城县人。卡尔曼株式会社(KARUMANG)代表董事长。在丰田汽车工业(株式会社)任职时,在成本、生产、采购部门追随大野耐一先生致力于“丰田生产方式“的实践、改善和普及工作。1984年以后,从事农业机械制造商、住宅开发商的“丰田生产方式”的实践指导工作。1991年任韩国大宇汽车的顾问。1992年成立卡尔曼株式会社。并担任西安交通大学的客座教授。著有《丰田生产力》、《丰田处世力》、《丰田工作哲学》等十余本有关丰田生产方式的作品。
丰田这个企业,曾陷入过多次危机,但是每次都能绝处逢生,同时实现巨大的发展。为什么会这样?那是因为,很多的企业在遇到危机时都是抛弃过去,否定过去。但是丰田却是回到原点以克服危机。正因为如此,丰田才能不断发展。 丰田生产方式的原点就是“改善”。现在,虽然“KAIZEN(改善)”已经成为一个世界共通的词语,但是并不存在指南或者国际规格。这是因为改善是在生产现场工作的每一个员工的智慧的积累。 在笔者看来,正因为如此,执行方法完全不对、执行不彻底的公司实际上有很多。掌握丰田生产方式的第一步,是从彻底的改善开始。 丰田的去除浪费Ⅰ 何谓“浪费” 浪费不能提高附加价值 要想了解丰田生产方式,有必要先了解一下什么是改善;要想了解改善,必须充分理解什么是“浪费”。 迄今为止,笔者已经协助多家企业进行过生产改革。其中,最让笔者困惑的是,关于什么是“浪费”,不同的企业,甚至不同的人之间都会有不同的理解。 对于“去除浪费”这一想法,毫无疑问不会有人反对。无论是谁,都清楚地知道,如果去除浪费,企业不但会提高生产力,还会提高利润。但是,如果对如此重要的“浪费”存在认识上的偏差的话,企业即使想要进行“去除浪费”,也是没有办法进行下去的。 例如,在仓库里摆放零件、零件原材料、成品等。看到这一场景,有的人会说:“这些就是浪费。”但有的人会说:“如果只有目前这些库存的话,既不会给顾客添麻烦,生产也不会停滞。”如上所述,面对这样的现状,即使企业发布削减库存的号令,也是进行不下去的。 如果换成是员工,也是一样的道理。 有一位员工每天起早贪黑地工作。看到他的表现,某一位上司将他的工作方法以及成果进行综合评价后,指出:“你的浪费太多了!”可是同时,也许会有别的上司夸奖他说:“你工作得很努力啊。”同样道理,不管企业怎样提倡员工去除工作中的“浪费”,工作方法也是不会改变的。 为了顺利推进丰田生产方式的改善,首先,关于“浪费”,大家的意见以及思考方式必须统一起来。那么,什么是丰田生产方式中的“浪费”呢? 简而言之,浪费就是指不能提高附加价值的一切现象和结果。在生产现场,可以理解为,只会提高成本的生产诸要素。 有效作业与无附加值作业 首先我们从作业的“浪费”开始。如果仔细观察工作现场的人的动作,可以将其区分为“作业”与“浪费”。进一步说,作业可以分为“有效作业”与“无附加值作业”。 1.浪费 作业中没有任何必要,只会提高成本的动作。有必要立即杜绝这种浪费,改善就需要从这里开始。 2.无附加值作业 不能提高附加价值的作业。本来,这也可以称之为浪费,但是在特定的作业条件下,也会有很多不得不做的工作。更换程序(作业内容或者生产品种发生变化时的作业)、去仓库取零件、找零件、解开零件的包装,诸如此类的作业。这其中当然存在着“浪费”,但是由于无法马上就将其省略掉,所以有必要进行作业条件的改善。丰田生产方式中最重要的就是,不将此类无附加值作业作为工作的一部分,而是将无附加值作业看作是应该被省略的“浪费”,并由此开始进行改善。 3.有效作业 能够提高附加价值的作业才被真正认为是生产。改善的重点是提高作业中有效作业的比率。丰田生产方式之父——大野耐一先生(曾担任过工厂厂长,历任副社长、荣誉顾问)曾经有过这样一个说法:“把动作当工作来做。”无论业者本人如何忙碌地工作,有效作业以外的都是“动作”,而不是“工作”。所谓“工作”是工程有进展、工作有成效的部分。为了减少浪费以及无附加值作业,就要将“动作”变成工作。 重新认识作业要素 如何才能及时发现“浪费”,提高有效作业的比率呢?首先是要将准备改善的作业分解为最小单位的“作业要素”。例如安装零件、按按钮、运输成品。针对这些作业,逐一展开讨论。“这个作业真的有必要吗?”“这个做法能不能再简单一些?”“为什么要用这个方法?”如果这样做,就能发现浪费,并且得到改善的启发。特别是对于管理监督者来说,需要有这样发现浪费的眼光。 监督管理者的工作,不是用夸奖“您干得真卖力啊”来鼓励作业工人,也不是激励他们说“要再加把劲啊”,而是认真思考“有没有更轻松的做法?”、“能不能再简化一些?”这些问题。 去除浪费,以更高效的工作方式作为改善目标,这才是丰田生产方式中监督管理者的工作。当然,作为监督管理者本人,如果认识到“费劲”、“痛苦”、“一定有更便捷的做法”这些问题,马上提出改善提案也是非常重要的。 如果大家对于浪费都有共同的认识、意识到需要改善、都考虑如何去除浪费的话,就会成为杜绝浪费的专家。监督管理者与作业工人如果不断积累这样的想法和提案,改善也就能水到渠成地开展,浪费也会逐步减少。 丰田的去除浪费Ⅱ 生产现场的八大浪费 不合格品和返工/生产过剩的浪费 接下来,我们将讨论生产现场的浪费。大体上可将其分为八大浪费。分别为“不合格品、返工的浪费”“生产过剩的浪费”“加工中的浪费”“搬运中的浪费”“库存的浪费”“动作的浪费”“停工的浪费”“产业废弃物的浪费”。毫无疑问,浪费存在于所有的部门中。从生产部门的八大浪费入手,必须认真思考在自己的部门中到底存在什么样的浪费。 1.不合格品、返工的浪费 是指生产了不合格品,使品质下降,或者因返工带来的成本增加。 在制造业中,实现不合格品为零几乎是不可能的。甚至有人说,如果想让不合格品率为零,那么根本就无法进行生产。在许多企业中,正因为有着对于“不合格品”的容忍,所以现状是,很多人将不合格品的返工也作为工作的一部分。但是,制造的基本就是“合格率百分之百”。如果认为“或多或少的不合格品也是没有办法的,只要进行修正就可以了”,那么实现合格率百分之百、无须修正这样的目标是永远也实现不了的。我们必须认识到,制造不合格品就是浪费,返工不是工作的一部分。 2.生产过剩的浪费 这是丰田生产方式中最应该提高警戒的浪费之一。生产过剩,不但会造成原材料的浪费,还会造成能源费用以及人工费用的浪费。更进一步讲,为保管生产过剩的产品而使用的仓库和人工也会产生新的浪费。如果产品不够,这当然是浪费,大家非常容易理解。但是生产过多是更大的浪费,会这样思考的人却是少之又少。但是实际上生产过剩一定会产生很多浪费。丰田生产方式的基本就是JUST IN TIME生产,即在必要的时间内,生产必要数量的必要产品。换言之,就是根据顾客的需求生产产品。 …… 丰田的修养Ⅳ 11 只有不断改善才能拥有竞争力 岔路口出现在成果刚开始有成效时 推进丰田式改善时,企业高层意志的第二个要点就是“继续”。如果已经开始着手改善,企业要努力做到最终将改善充分根植到企业文化中去。 着手进行丰田式改善的企业一般有两种模式。一种是,经营比较顺利,但是由于抱着“这样下去是不行的吧?”这种危机感而着手进行改革。另一种是,面临真正的赤字危机,背水一战地进行改革。 虽然丰田生产方式,强调在经营顺利的前提下就进行改革,但是实际情况却是,大多数企业都是在经营面临赤字的时候才考虑进行改革。不管是哪种前提,都将在丰田生产方式中找到出路,同时,如果企业高层保持高度的热情,努力进行改革,大多数企业都可以在一年左右就感受到丰田生产方式的实际效果。 为什么会有如此成效,那是因为很多企业的制造方法中包含了过多的浪费。仅通过彻底地进行整理整顿,就能实现如此的效果。某一电力工程公司就是一个典型的例子。企业仓库以及工程用车车辆内部堆积了如山的库存,在进行整理整顿之后,就产生出了数千万日元的利润。 该企业进行了整理整顿后,由于又进行了制造方法的改善,因此不合格品减少了,交货日期也缩短了,最终在连续赤字一年左右就实现了扭亏为盈。大家最终也都感受到,必须进行改革。这样的状况如果持续两年、三年,利润提高后,企业内部也会发生变化。 企业在面临严峻的危机或者持危机感时,无论是经营者还是企业员工都会努力实施改革。但如果利润得到了切实的提高,“改善之手”就会松弛下来。因为很多人会认为:迄今为止已经非常努力了,既然获得了这样的成果就可以稍微休息一下了。这里也就会成为改革的岔路口。