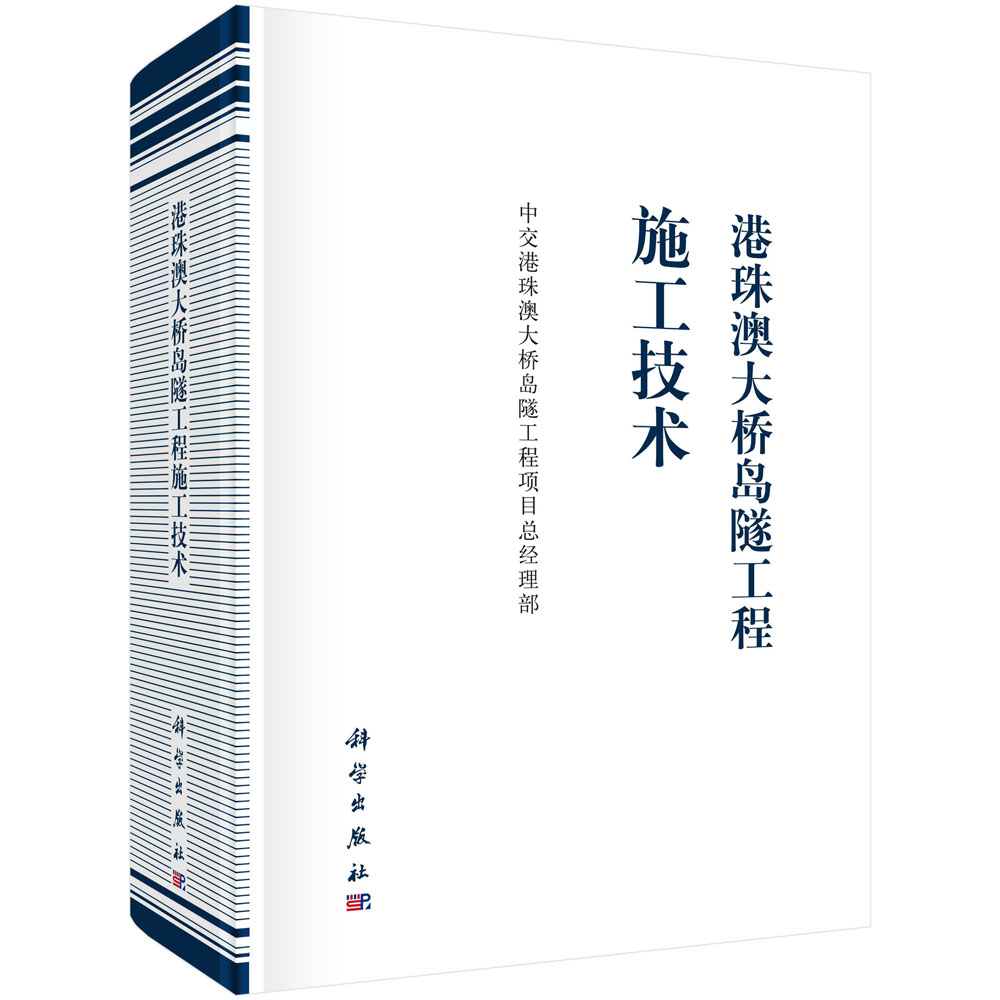
出版社: 科学
原售价: 398.00
折扣价: 314.50
折扣购买: 港珠澳大桥岛隧工程施工技术
ISBN: 9787030682925
第1章 绪论
1.1 世界沉管隧道发展概况
1910年,跨越美国与加拿大之间的底特律河水底铁路隧道建设完成,这是世界上第一条沉管铁路隧道,采用双层圆形钢壳结构。1942年,荷兰在鹿特丹修建完成了马斯河水下公路隧道,这是世界上第一座混凝土沉管隧道。我国香港地区于1972年建成了跨越维多利亚港的红磡海底隧道,到了20世纪90年代初,广州、宁波两市的沉管隧道相继建成通车,其中1993年建成通车的广州黄沙至芳村珠江隧道,成为我国大陆第一座城市道路与地下铁道共管设置的水下隧道。
2010年以前,全世界已经建成了一百多条沉管隧道,然而,长大型沉管隧道发展缓慢,中国大陆在该领域技术更是空白,只有小型跨江、河沉管隧道建设经验,当时世界著名的三个大型沉管隧道工程是丹麦厄勒海峡沉管隧道、韩国釜山—巨济沉管隧道和土耳其博斯普鲁斯海峡沉管隧道,它们的特点如下。
1. 丹麦厄勒海峡沉管隧道
2000年建成,隧道长3510 m,钢筋混凝土结构,其特点:
①大型跨海沉管隧道。
②工厂内控制环境下预制。
③固定模架全断面浇筑。
④先铺碎石基础。
2. 韩国釜山—巨济沉管隧道
2010年建成,隧道长3240 m,钢筋混凝土结构,其特点:
①大型跨海沉管隧道。
②干坞内露天环境下预制。
③移动模架全断面水准浇筑。
④先铺碎石基础。
3. 土耳其博斯普鲁斯海峡沉管隧道
2008年建成,沉管隧道长1387 m,单侧钢壳钢筋混凝土结构,其特点:
①大型跨海沉管隧道。
②干坞內浇筑下半段管节。
③临码头边浮态灌注上半段管节。
④混凝土管节 + 外包钢板。
⑤岸侧盾构机直接与沉管对接。
⑥超深水、复杂水流环境。
⑦先铺碎石基础。
1.2 珠江口跨海通道建设
改革开放以来,珠江三角洲区域发展迅速,东、西两岸发展急需寻找新的空间,共谋协调发展。早在1983年,国家首次提出了连接香港和珠海的一座跨海大桥方案,即伶仃洋大桥方案。后来香港的青屿干线通车,大桥香港起点改为大屿山,原伶仃洋大桥计划搁置,改名港珠澳大桥。但由于港珠澳大桥不与深圳连接,无法解决深圳连接珠江西岸的需求,于是连接深圳市与中山市的公路通道—深中通道也获批立项。
截至2020年,珠江口区域完工和在建的4条通道分别是:1997年建成的虎门大桥;2018年完工的港珠澳大桥;2019年完工的南沙大桥;2016年底开工的深中通道。其中,港珠澳大桥为最靠下游的跨海通道,也是我国首例跨海大型沉管隧道工程。
1.3 港珠澳大桥简介
港珠澳大桥东连香港、西接珠海/澳门,主体工程由粤港澳三地合作建设。珠江口是中国航运最为繁忙的海域,也是世界上最繁忙的航道之一,主航道紧邻香港国际机场,由于受香港国际机场限高控制,大桥在主航道处采用了沉管隧道工程,是大桥的控制性工程。
港珠澳大桥全长约55 km,其中主体工程“海中桥隧”长35.6 km,粤港澳三地共同建设的主体工程长约29.6 km,香港段长约6 km。桥址东起香港大屿山,接香港口岸,经香港水域,穿(跨)越珠江口铜鼓航道、伶仃西航道、青州航道、九洲航道,止于珠海/澳门口岸人工岛。港珠澳大桥总平面图如图1-1所示。
图1-1 港珠澳大桥总平面图
港珠澳大桥工程采用桥隧组合方案,穿越伶仃西航道和铜鼓航道段约6.7 km,采用沉管隧道方案。为实现桥隧转换和设置通风井,主体工程隧道两端各设置一个海中人工岛,东人工岛东边缘距粤港分界线约366 m,西人工岛东边缘距伶仃西航道约2000 m,两岛长度均为625 m,两岛间沉管段长5664 m,管节数量33节,具体如图1-2所示。
图1-2 港珠澳大桥沉管隧道图
1.4 港珠澳大桥岛隧工程主要技术难题
2002~2011年中国完成了4座著名跨海大桥:东海大桥、杭州湾跨海大桥、舟山大陆连岛工程和青岛海湾大桥的建设,这4座跨海大桥的长度都达到了30 km左右,建设技术水平均达到了国际领先水平。
然而发展至港珠澳大桥,总长度达50 km以上,且为桥、岛、隧一体综合性复杂的跨海通道工程,是中国首例跨海沉管隧道,也是世界唯一的深埋沉管隧道及最长的公路沉管隧道工程。应该说,当时的国内已有了跨海桥梁及跨江、河小型沉管隧道技术经验,但像港珠澳大桥岛隧工程这样的超级工程,仍有诸多技术是空白的,主要挑战有:非常差的岩土条件,地基的软土厚度达30~50 m;恶劣的气候和波浪条件;沉管隧道的埋深超过20 m,荷载是一般沉管隧道的3~5倍;要在回淤环境下完成近6 km深水基础的施工;单节沉管安装重量约7.8万t;沉管沉放深度接近50 m;等等。
可以说,港珠澳大桥岛隧工程是当时世界上最具挑战的沉管隧道工程。这个挑战,需要超越当时最先进的工程领域技术和经验,具体包括以下几个方面。
1.4.1 人工岛
为了最大程度减小施工对珠江口生态环境的影响,初步设计方案变更为深插大直径钢圆筒基坑围护结构施工。西人工岛钢圆筒61组,钢圆筒设计桩长40.5~50.5 m;东人工岛钢圆筒59组,钢圆筒直径22 m。主要难点如下。
1. 深插大直径钢圆筒施工
①离岸宽阔海域施工,受风浪影响大。
②最大水深16.5 m,钢圆筒设计长40.5~50.5 m,运输、施工时钢圆筒稳定性差。
③钢圆筒直径大(22 m),要插入海床近50 m至不透水层,振沉难度大。
④钢圆筒兼作人工岛基坑围护结构,水密难度大。
2. 深插式塑料排水板施工
两岛钢圆筒围护结构内侧区域均需打设塑料排水板,正方形布置,间距1 m。泥面标高?18 m,排水板底标高最深为?46.0 m。
①塑料排水板打设为陆上施工,打设时需穿透上部的回填中粗砂层、回填碎石层,最大插板深度为40 m,打设难度极大,以往没有陆上打设40 m深的塑料排水板。只在澳门国际机场的软基加固工程中使用过塑料排水板,塑料排水板穿透了23.5 m厚回填砂层和12 m厚黏土层,总插板深度35.5 m。
②人工岛施工面窄,塑料排水板总量大,约500万m3,施工工期短,施工机械多。
针对以上难题,项目团队全球首创深插大直径钢圆筒作为人工岛岛壁兼作基坑围护结构的全新快速筑岛技术,首次采用八锤联动液压振动锤进行振沉施工,快速形成陆域,实现了止水和围护结构一体。利用整岛止水条件,快速启动大超载比预压进行岛内软基处理和深基坑开挖,实现了岛内、岛外同步施工,为沉管隧道止推段施工及岛上结构物建设提供了条件。
采用该项技术,221天完成东、西人工岛120个钢圆筒振沉,筑成两个10万m2外海人工岛,节约工期2年半;现场只有包括钢圆筒运输船、定位船、钢圆筒打设浮吊船等不到10艘施工船舶,仅为采用传统技术施工需要船舶数量的1/10,极大降低了通航风险;避免大规模海底淤泥开挖,减少泥沙开挖量近1000万m3,树立了绿色、安全、高效施工新典范。
1.4.2 隧道基础
港珠澳大桥沉管隧道软土地基厚度达40 m,远超以往同类工程,在国内,该领域以往的施工经验已经不能覆盖。
1. 基槽开挖精度控制
沉管隧道基槽长5664 m,最大深度近50 m,最大开挖厚度35 m,基槽开挖精度对边坡稳定及隧道基础质量影响大,是沉管隧道安全运营的关键。主要难点如下。
①基槽开挖最大容许超深0.5 m、最大容许超宽2.5 m,精度要求高,超过了以往所有类似工程控制标准,具有很大的挑战性。
②横流作业,边坡及超宽精度控制难度大。
③潮汐、波浪、水流共同作用对开挖深度控制影响大。
④纵向连续变坡,精度控制实施难度大。
⑤由于自然水深变化比较大,外加纵坡影响,导致开挖形状不规则,对施工船舶质量控制和施工效率制约比较大。
2. 地基加固
通过方案比选,在人工岛、岛头结合部及过段沉管段采用挤密砂桩地基加固方案。砂桩直径1600 mm,最大入土深度27.2 m,需穿透2~5 m厚平均标贯击数8.7击的②1黏土层,进入平均标贯击数4~12.9击的第③层土层。主要难点如下。
①工程地质复杂,国内外无在较硬的地层上施工挤密砂桩的先例。
②挤密砂桩总量约50万m3,远大于以往类似工程规模。
③东、西人工岛作业面窄,工期紧,施工组织难度大。
3. 基槽清淤
工程区域海水平均含沙量0.012 kg/m3,最大含沙量0.141 kg/m3。汛期含沙量变化、附近航道疏浚及采砂作业、大型运输船舶对底质的扰动及异常恶劣天气等均引起基槽回淤加大,施工过程中E15就遭受了严重回淤情况,带来了极大的风险和工期损失。主要难点如下。
①改变碎石基床受力特性,影响基床结构的传力效果。
②基床面淤积,造成沉放管节无法着床。
③对沉积物的扰动,改变海水容重,影响已安管节的抗浮安全。
④导致沉管工后沉降过大及不均匀沉降超标。
4. 碎石基床整平
近50 m水深,碎石基床整平后高程误差≤40 mm,单个管节相邻整平船位内碎石垄顶测点平均值≤20 mm。主要难点如下。
①整平精度要求高。
②需要适应工程要求的专用整平设备。
③施工作业效率受风浪影响大。
为减少工后沉降,实现沉管隧道地基刚度平顺过渡,在隧道基础设计中采用了复合地基的设计理念,对东、西人工岛隧道过渡段地基进行了多种形式的加固处理。其中采用SCP + 堆载预压地基加固技术填补了国内软基处理空白。针对深厚软土层隧道基础,首创了复合地基 + 组合基床的隧道基础新结构,采用了“抛石夯平+碎石整平”的组合垫层设计方案。研发的沉管基础施工质量检测监测管理系统、外海堆载预压监测系统、沉管隧道沉降变形监测系统,有效保证了基础施工过程质量。经持续监测,建成后的沉管隧道平均沉降仅7.4 cm,差异沉降小于1 cm,达到国际领先水平。
1.4.3 管节预制
港珠澳大桥海底隧道沉管,标准管节重约7.8万t,采用“工厂法”预制,且这是世界上首次采用曲线沉管工厂法预制工艺。主要难点如下。