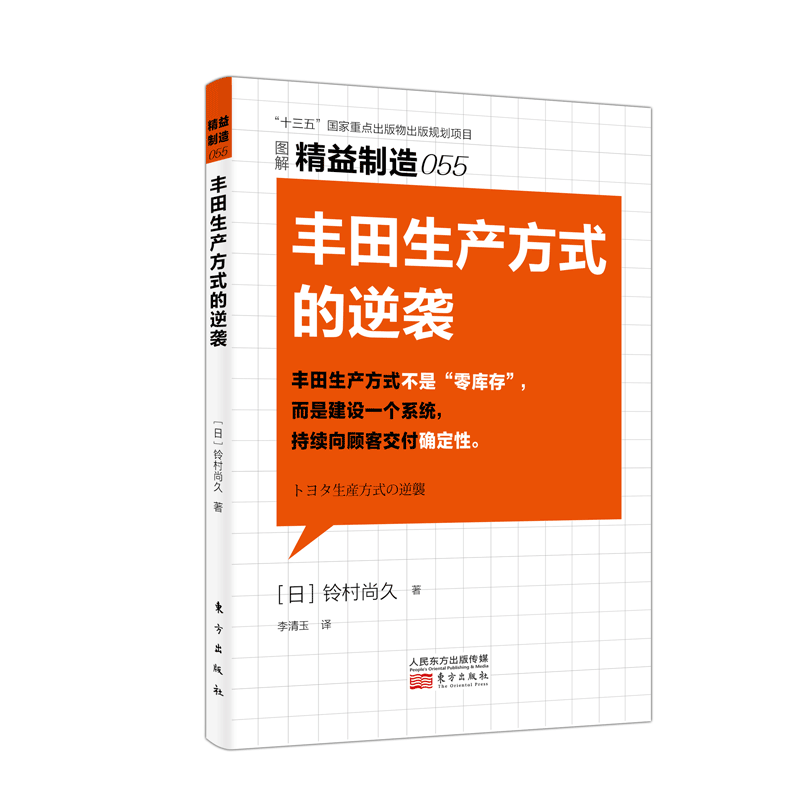
出版社: 东方
原售价: 58.00
折扣价: 37.70
折扣购买: 精益制造055 :丰田生产方式的逆袭
ISBN: 9787520704731
1952年生人。1976年从京都大学法学部毕业,后进入丰田汽车工业(现名丰田汽车)。曾在公司财务部、第二购买部、产业车辆部、生产调查部、销售店业务部以及日本国内企划部任职。1997年退休。1999年,成立FPM研究所。其父喜久男先生(已故)为“丰田生产方式”的创始人——大野耐一先生的左膀右臂。
只追求流于表面的成本缩减. 反而最后导致了成本不断追 高. 近年来. 这样的例子在产业界内俯拾即是. 最典型的例子就是只考虑缩减人工费用. 不假思索地将工 厂移设到海外. 但由于交付期以及品质等问题. 只能在日本国 内谋求解决之策. 也存在虽然实施了一些提高生产积极性的作 业改善. 但对于开发、销售以及物流等部门的白领阶层的生产 积极性改善却熟视无睹的情况. 此外. 还有一些和我专业领域相关的案例. 有的企业由于 过度解读“ 丰田生产方式的绝妙之处在于没有库存” 这一点. 不仅放弃了必要的库存. 给顾客造成了困扰. 还使销售额以及 利润大幅缩水. 为什么会有如此多的失败案例呢? 那是因为企业进行了以错误规范为基础的“改善活动”? 虽 然看起来顺应时势? 应用着非常先进的自动化、IT 化处理流程? 但由于制造方式陈旧? 不适应时代需要? 因而造成了企业库存 过多? 甚至阻碍现金流动使得财务方面的情况不断恶化? 比如说? 为了让产品更有效率地流向市场? 企业采用电脑 化管理? 建设了现代化的物流仓储? 即便如此还是时常发生交 付期拖延的现象? 那么这就不是“物流” 而是“物留” 了? 现 代化的仓库与工厂陈旧的生产方式、销售部门蹩脚的销售手段 无法协调配合? 从而使企业陷入了尴尬境地? 迄今为止? 我还没有在媒体上公开过自己的言论? 可以说? 一直以来我是有意识地回避的? 因为我觉得经营顾问作为“ 幕 后” 工作者? 似乎不适合在公众场合抛头露面? 然而? 这一次我出于某些原因改变了一直以来的信念? 说 服自己执笔著书? 最近? 我发现关于丰田生产方式有许多离谱的解答? 尚未 理解丰田生产方式的本质就将其导入企业内部却迟迟不出成果 的公司并不少见? 有时我想? 能否凭借自己的微薄之力改变这个趋势呢? 慢 慢地这个念头在脑海中再也挥之不去了? 我是1976 年(昭和五十一年) 进入丰田汽车工业的? 这也 是作为社会人迈出的第一步? 在我进入公司的三年前? 日本经 济由于石油危机大为受挫? 1974 年日本战后经济史上首次出现 了负增长? 也可以认为这是日本经济的一个转折点? 不过幸运 的是? 我进入公司的时候? 日本经济已经开始重振旗鼓? 显现 出了复苏的迹象? 1976 年? 大和运输公司旗下的快递产业的新 兴? 东急手创馆的成立等? 让新型消费形态不断出现在人们的 生活里? 丰田生产方式也是在那时开始受到世界广泛关注的? 石油 危机让许多一流企业跌落神坛、赤字频现? 只有丰田持续盈利 并且以惊人的速度恢复到原先的经营状态? 为了探索其中的奥 秘? 许多学者以及媒体开始关注丰田的制造方法? 亡父是丰田的员工? 是土生土长的爱知县丰田市人? 从前 经常听他说起丰田的历史? 其实当初我进入丰田的保证人就是 丰田生产方式的“ 创始人” 大野耐一副社长( 当时任职)? 我 的父亲可以说是大野先生的左膀右臂? 为丰田生产方式的确立 立下了汗马功劳? 父亲的存在也被学术界知晓? 在? 丰田系统 的原点? (文真堂? 下川浩一、藤本隆宏编著) 等书中也屡次提 到了父亲的名字? 父亲不仅在企业内部指导了丰田生产方式? 并且也对合作分包企业进行过指导? 退休之前一直是丰田生产 调查室的主要调查人(部长级别)? 退休后转战经营咨询顾问? 父亲于1999 年逝世? 时年73 岁? 这里提到的“ 左膀右臂”? 意思是父亲在以大野先生为中 心? 将丰田创始人丰田喜一郎所倡导的理念——— “ just? in? time” (将必要的产品在必要的时候生产必要的量) 这个理念体 系化的过程中作为“实行部队长” 亲力亲为? 在拙作中有很大 一部分来自父亲的描述? 我希望以这些描述为基础? 继承发展 下来? 虽然我并没有亲自接受过大野先生的指导? 不过在进入公 司不久后和他见面的情形现在依旧留存在我的记忆中? 大野先 生在视察的时候我跟随过几次? 那个时候? 他注视着生产线一 直用洪亮的嗓门重复说着“不明白? 不明白”? 这似乎是他的一 个口头禅? 操着一口三河口音? 不停地向部长、科长质疑? 一 来一回仿佛佛禅问答一般? 实在有趣? 这句“不明白”? 在丰田生产方式中占据非同寻常的地位? 这一点我也是很久以后才明白的? 什么样的产品才是真正被需要的产品? 才需要生产必要的 量呢? 究竟怎样作业是合适的? 交付期是什么时候? 生产线的工作状况是正常的? 还是异常的? ———这些问题必须让大家一目了然? 这样? 不仅可以在发 生品质等问题的时候更容易找到线索? 还会让解决之策更加 清晰? 最近? 有很多书都在说明工作现场“ 可视化” 的重要性?其中不乏介绍丰田的工作方式特征———为何重复五次等的内容?这些书本中理论的根源都离不开大野先生的一句“不明白”? 以 及其中的思维方式? 同时? 在丰田内部非常受到重视的“5S”(整理seiri、整顿seiton、清扫seisou、清洁seiketsu、素养shit ̄suke) 也一样? 如果不把工作环境打扫干净? 其中的问题点就很难显现出来? 这也是面对“不明白” 时的一个解决对策?丰田生产方式也被称作“TPS (Toyota Production System)”?现在已经普及海外? “ kanban ( 看板)” 以及“ kaizen ( 改善)”等的一些关键词组也翻译成了英文? 并且? 不光是制造业? 丰田生产方式还被广泛地应用到了医疗等行业的经营中?丰田生产方式是地地道道的“ made in Japan” 的经营理念?这一点毋庸置疑? 然而? 丰田生产方式的原点并非日本? 而是美国? 然而很多人都没有关注过这个事实? 丰田生产方式不是“零库存”,而是建设一个系统,持续向顾客交付确定性