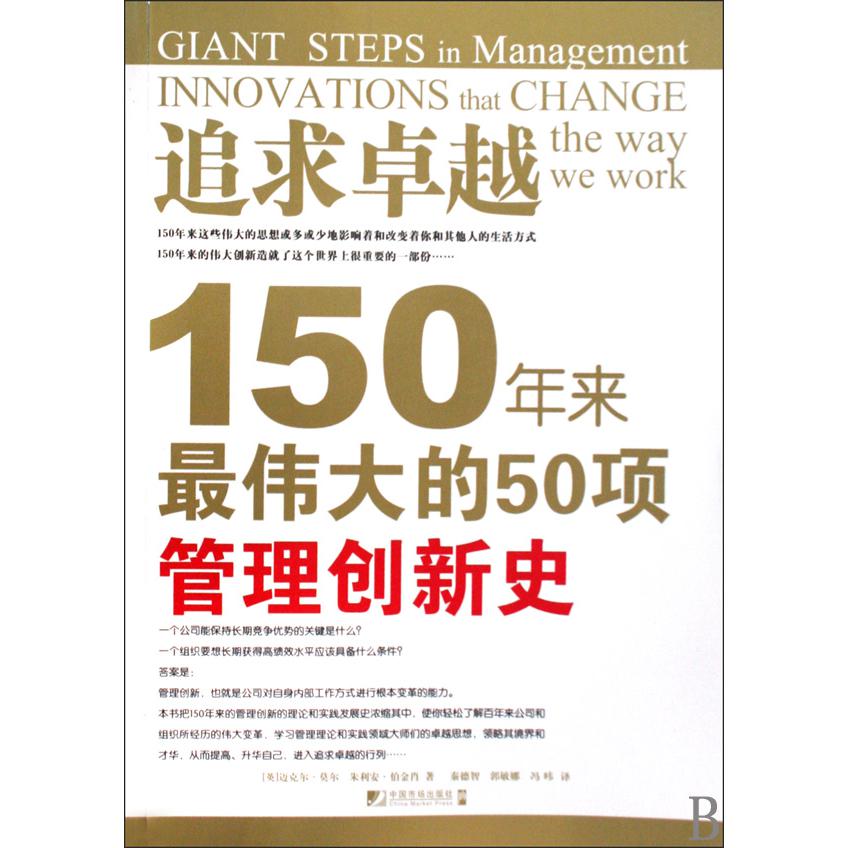
出版社: 中国市场
原售价: 48.00
折扣价: 35.06
折扣购买: 追求卓越(150年来最伟大的50项管理创新史)
ISBN: 9787509206225
朱利安·伯金肖(Julian Birkinshaw),伦敦商学院战略与国际管理系的教授,管理创新实验室的创立者之一。他是研究大公司如何培养企业家精神和创新意识的权威,出版了十本著作,包括《风险投资》、《跨国公司中的企业家精神》和《斯文-戈伦·埃里克森的领导方式》等。 迈克尔·J.莫尔(Michael J.Mol),雷丁大学战略管理方面的高级讲师伦敦商学院管理创新实验室的访问学者。他是大公司战略管理方面的专家,研究方向为采购战略和管理创新。出版了三本著作,包括最新出版的《采购外包:设计、流程和绩效》。
丰田生产方式 大野耐一从机器的安排上开始了他的实验:“这是对将大量相同部件在 同一流程上生产出来并运往下一个流程这种传统系统的根本性改革。1947年 ,我们将机器安排成并行的平行线或者是L型,并且让一个员工可以同时操 作处理路径上的三四个机器。”经过努力,最后这种新的生产方式被接受, 而随后供应商们也被安排到新产品的开发流程中来: 我们想改变以前大量生产直到月末的这种方式,于是我们从丰田内部开 始着手。当需要外部供应商时,我们首先了解需求并要求供应商与我们合作 实现均衡化生产,并且我们还根据情况变化就劳动力、原材料和资金方面与 合作供应商进行讨论。 这与看板管理一起减少了库存量并保证了更有效的产品流动。1953年准 时制生产系统应用于每个机械加工车间,而看板管理直到1962年才运用到整 个公司。 此系统最初无法解决的问题是快速且无法预期的需求数量和性质变化。 因为太多的计划需要制订,所以即使是微小的变化也可能在很大程度上影响 整体绩效。丰田通过重新编排经销商的订货顺序解决了部分问题,其中包括 有时更具侵略性的销售手段的使用。丰田面临的另一个问题是产品质量。为 了满足美国陆军的质量要求并且将自己的皇冠车型出口到美国,丰田于1958 年建立了全面质量控制系统,这种系统后来发展成为家喻户晓的全面质量管 理。 模仿精益生产 丰田花了很长时间来发展和实施这种生产系统,当外界开始意识到这种 系统有多么成功时,其他人早已开始模仿甚至是使用相似的系统。丰田及其 他日本公司悄无声息地抢占了全世界汽车市场的大部分市场份额。20世纪70 年代末,西方学者开始渐渐关注日本汽车业的发展。 学者沃马克(Womack)、鲁斯(Roos)、琼斯(Jones)在其1991年合撰的著 作《改变世界的机器——精益生产传奇》中描述了当时丰田的精益生产模式 。1986年当他们前往位于日本高冈市的丰田装配厂访问时,感到非常吃惊: 在焊接处扣油漆点以及油漆点和最终组装处几乎没有任何缓冲衔接,也 根本没有任何零部件仓库,因为供应商刚生产出来的零部件每隔一小时都以 准确的需求量被运往生产线上。 他们同样也将丰田厂的精益生产与通用汽车的弗兰明翰(Framingham)分 厂的大规模生产模式进行了比较: 在生产标准化汽车并执行同一套标准活动时,高冈厂是弗兰明翰厂产量 的两倍,而精确度达三倍。就制造场地的利用率而言,高冈厂比弗兰明翰厂 的利用率高40%,而存货却仅仅是弗兰明翰厂极小的一部分。 从20世纪80年代初开始,一些西方汽车制造商开始模仿丰田的生产模式 ,新联合汽车制造公司(NUMMI)就是其中之一。它是基于20世纪60年代建立 的位于加利福尼亚的通用汽车工厂改建的,由丰田公司和通用公司建立的合 资公司。沃马克、鲁斯、琼斯发现: 新联合汽车制造公司能够达到丰田高冈厂的汽车质量和生产力,但是工 厂场地利用率因为通用汽车厂以前的布局不合理而达不到高冈厂的水平。同 时库存量也比高冈厂高出许多,这主要是几乎所有的零部件都要跨越太平洋 经过5000英里才能运输到,而高冈厂只需要从高冈市附近的供应商,经过5 或10英里就能运输到。到1986年,我们都能清楚地看到丰田确实在制造业改 革中取得了巨大的成就,旧的大规模生产模式已经不再具有竞争力,而新的 最有效方法——精益生产也能够很好地转移运用到新的环境中,比如新联合 汽车制造公司。 但是通用公司最终并没有从新联合汽车制造公司学习到很多精益生产模 式,而且其他诸如福特汽车等公司在采用精益生产模式上也是苦苦挣扎。 精益生产的普及 如今,精益生产已经在制造业得到了广泛的发展,从中国的自行车制造 、意大利的橄榄油提炼机器建造,到伦敦的地铁网络升级。一些政府也积极 推进精益生产在当地企业的应用,“精益”的概念也被运用到创新等其他业 务流程中。 在小企业和服务行业方面,也逐渐开始应用精益生产。有趣的是,当初 精益生产思想来源,比大野耐一的研究早50多年的超级市场现在也开始学习 丰田模式。精益之所以这么有影响力是因为它体现了生产流程的本质:运用 尽量少的成本生产尽量多的产品。 全面质量管理 质量毫无疑问是产品的一个重要特征,如果产品质量得不到保证,那么 产品就不能令人相信,顾客也会很轻易地略过它不作考虑。20世纪50年代日 本的产品质量急需得到提高,因为自从二战以来,日本丧失了大部分的生产 力、资源及在世界的地位。二战后日本制造业无法适应从生产军事用品到大 众用品的突然转变,日本产品质量也非常低劣,尤其是与美国制造的产品比 较而言,于是国外基本找不到标有“日本制造”的产品。 同时由于日本的国内需求很小,增加产品出口就成为日本企业成功的关 键。当时丰田和其他企业的精益生产为这些问题的解决提供了一丝希望,但 尽管精益生产最终极大地提高了生产效率和产品利润,它却并没有提高日本 的产品质量水平。事实上丰田的核心产品当时面临着严重的质量问题,这使 得它将国内市场的领先地位让给了日产汽车公司(Nissan),丰田只好暂时完 全转向美国市场。那么这些日本企业是如何提升其产品质量标准的呢? 零缺陷生产 解决上述问题的方法是全面质量控制(TQc)的引入,现在我们习惯称之 为全面质量管理(TQM)。全面质量管理旨在提高产品和服务的质量及组织效 力,它是建立企业内部产品质量持续提升的要求、确定每个员工所需完成的 质量责任目标的综合方法。质量目标水平首先由消费者来定义,最终目的是 要达到零缺陷生产的质量水平。持续的流程改进对产品零瑕疵的实现至关重 要,统计学上为测量次品及其原因提供了一些方法。 全面质量控制的日本创始人之一石川馨(Kaom Ishikawa)的著名的生产 五目标是指:先保证质量再求利润;通过培训激发员工的潜能,提供积极的 反馈和责任下放机制;进行长期的客户定向;充分利用方法和数据,并在全 公司范围进行交流讨论;开发一套员工能理解并承担产品质量后果的全面质 量控制系统。根据石川馨的观点,生产最优品质的产品需要“全公司每个员 工共同承担责任”。因此与其关注事后检查,不如通过所有员工和管理者的 努力做到次品的事前预防,不管在生产过程中、其他支持功能上还是供应商 管理方面,都要做到次品的事前防范。 P25-28